
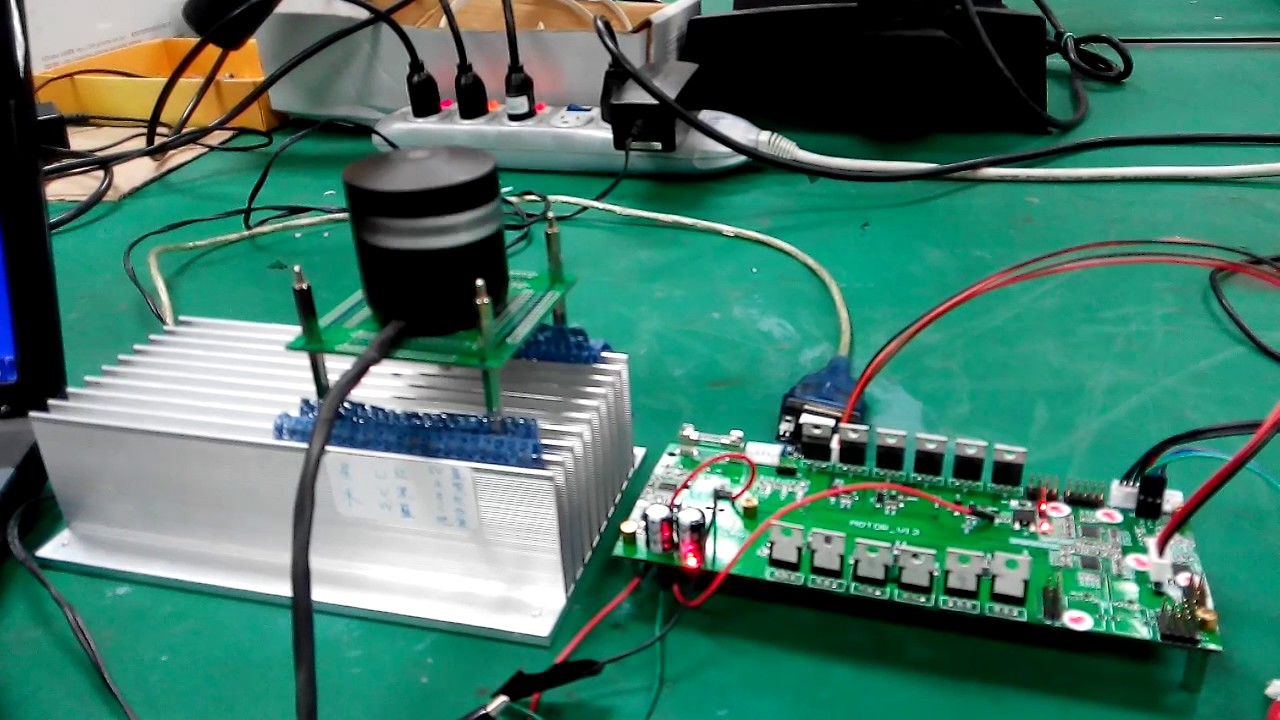
This is a challenge because a special hardware controller/driver is needed, along with the programming to make it work. However, many if not most products will require a custom design. The motor stator windings are driven by three MOSFET half-bridges.įor some designs, you could use a pre-programmed and packaged BLDC motor-control module, which may be satisfactory for certain common applications. FOC is a sensorless method that reads the trapezoidal-shaped feedback voltages from the motor stator windings and then processes that feedback into control signals for the motor.

One emerging control technique is field-oriented control (FOC). These signals are sent to the controller that generates the three-phase pulses applied to the stator coils. Other control approaches and algorithms are available, such as a sensorless method that uses the back electromotive force (back-EMF) induced into the stator coils by the rotating rotor magnets. BLDC motors typically use several sensors like Hall-effect devices to produce signals that are used by the controller to keep the stator-coil magnetic fields moving.
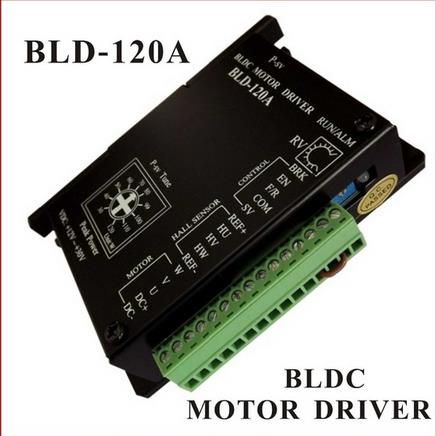
The control circuitry driving the stator coils get their correct timing from sensors that indicate the rotor’s orientation. The occurrence of the pulses must be timed so that they interact with the permanent magnets. Then a sequence of pulses is applied to the stator coils. A rotor consisting of multiple permanent magnets rides and rotates inside the stator coils. The stator coils are usually wired into three groups, making it a three-phase motor. Typically, multiple stator coils are embedded around the periphery of the BLDC motor assembly. Motor ControlĪ BLDC motor works like most other motors in that its rotation is produced by the interaction of two magnetic fields, one fixed and the other movable. Some examples, which may be similar to your project, include robotic vacuums, fans, pumps, washers, air purifiers and humidifiers, and multiple automotive devices. MCF8316A: Sensorless FOC integrated FET BLDC driverīLDC motors have assumed many of the jobs that older brushed dc motors and some ac motors once reigned over.3 ways to speed cycle time when designing with brushless-DC motors.
BLDC MOTOR DRIVER CONTROLLER DRIVERS
Reduce audible motor noise with BLDC motor drivers.Search and filter, then order what you need with a couple of clicks. Sourcing a bldc motor driver has never been simpler. If you need that level of precision, search 's listings for exactly the right stepper driver. Some drivers are tailored to specific machinery, including specialist models for 3D printers, while others go beyond standard drivers by allowing "microstepping" functionality. For instance, some take DC current and convert it to another DC voltage, while others deal with AC current and turn it into the DC current that motors require. Various types of motor driver can be found at the wholesale store, and the one you choose will depend on your specific needs. A bldc motor driver may well be essential when running advanced lightweight motors in electronic equipment and industrial machinery, and they are often needed when experimenting with motor kits like Arduino as well. Drivers supply that power, converting low voltage levels to higher levels, and doing so in a way that's dependable and secure. That's because the circuits motors are connected to often run on low current levels, while motors need more power. Without a motor driver in place, many motors simple wouldn't be able to function. Find exactly the right bldc motor driver model from 's extensive wholesale collection. So they are a valuable addition to many motor setups. They can supply extra control for stepper motors if precision is required, work according to programmable settings, and make sure that motors aren't damaged by current overloads. Motor drivers are devices which control electronic motors, and provide a shield between motors and sources of power. Create a rock solid link between motors and circuits with the motor driver collection at.
